

I've a lot of respect for Honda engineering, having had a couple of their cars. Honda engineers know more than I, so hence no solder on small gauge wires. Interestingly, Honda Motor Company do NOT recommend soldering terminals on any wire subject to flex or vibration due to solder creep under the insulation adding a stress riser to the wire inner core, and subsequent mechanical failure of the core strands. but in my experience, that doen't stop the bracing sea air bugring stuff up! are there actually any examples of wire failing by fatigue having been soldered? Also idea of nice long HS for strain relief is good, and adhesive lined - thanks very much! re wetness - all the wiring will be inside apart from the mast, won't get wet per se. Yes, I remember hearing hearing soldering wasn't the best idea but couldn't remember the reason! but as you suggest vibration on a boat isn't the same asa motorbike for example.

I'm glad at least one other person does the same,thanks for the tip on uninsulated connectors. you might have more luck using bullet connectors rather than spades? but that to me sounds like more faf than soldering it up.
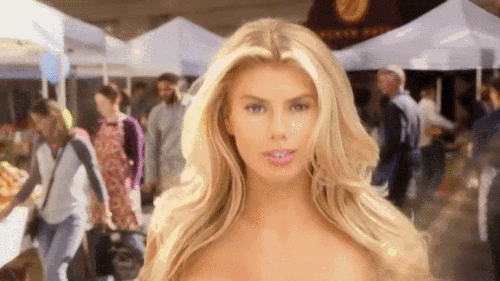
To seal up the entire connection like this you could put a few layers of smaller heatshrink over the crimped bit to bulk it up so that you can then use the larger stuff to go over the entire connection. The idea behind soldering them on is a) to improve both electricla and mechanical connection, and b) so that you don't need to stretch over the whole connector to seal it up, as there's no path down through the crimp. Get a decent soldering iron BTW, particularly if you're going to use dolphin-friendly unleaded solder! I would recommend a temperature controlled type, with a pretty hot bit. How wet will your wiring get? On motorbikes, vulnerable connectors can be helped a lot by filling them with vaseline or silicone grease.Īs you say, the extra time is small, it will pay off in ten years time. Make the heatshrink about 40mm long to provide some strain relief to the wire. If you do go the heatshrink route, go for adhesive lined heatshrink, it seals much better. Its better than relying on an amateur crimp tool, imho. Having said that, soldering is pretty much fine for a boat, if you take reasonable steps to secure the wiring. Crimping, done, properly is more reliable on its own, in a vibration environment, as soldering may make the cable too rigid just beyond the terminal. If you use a good quality, probably ratchet action, crimp tool properly, then soldering is superfluous.
